Are you interested in the difference between a regular cutterblock fitted with HSS knives and a spiral cutterblock fitted with HW knives? We have prepared a comparison of these in today’s test.
Veľa remeselníkov, ktorí používajú planers and thicknessers fitted with a cutterblock have unanimously agreed they no longer want to plane with a conventional cutterblock.
And because we are interested in reality, we have decided to do several tests to make sure of the advantages of a spiral knife cutter block.
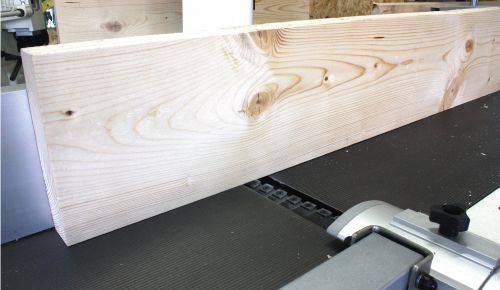
How will the cutter blocks deal with knaggy wood?
Conventional planing knives are the ones most frequently used among carpenters. They are an inexpensive option offering baseline quality. The cutter block usually comes fitted with three or four HSS knives. You don’t need to worry about the number of fitted knives as a lower number doesn’t necessarily mean lower quality. Manufacturers usually balance the lower number of knives with higher speed and the results are the same. The disadvantage of this type of cutter block is the difficulty of proper setting of knife height (read the article: How to properly fit knives into a cutter block?), which is a very important factor having an impact on the results of your work. You will need patience, time and accessories to properly set up your planing knives. Rapid dulling of the knives is another disadvantage, especially when planing hard materials. The last drawback worth mentioning is the generated resistance when planing wide pieces, which gradually increases with the dulling of your knives and width of the worked material.
Cutter block fitted with HSS knives
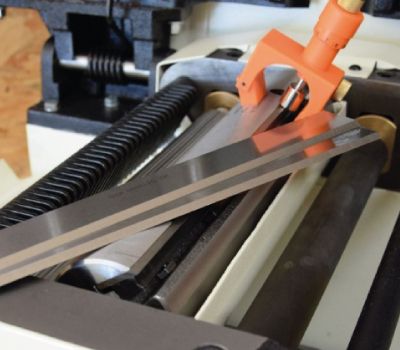
Cutter block fitted with HW knives
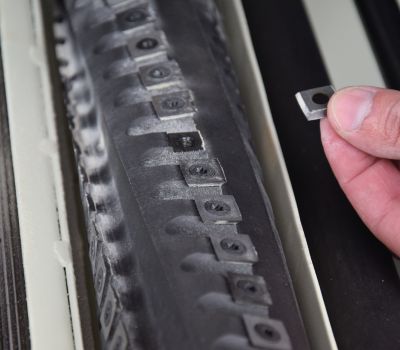
The spiral knife cutter block is really distinguishable. It's mounted with 15x15mm carbide knives, set in precisely milled beds. The setting of knives secures their firmness. The knives are set into four spiral rows. They imitate spiral router cutters, which are superb when it comes to cutting. Radius cutting edges secure a smooth surface job, good transition among the knives and create a levelled surface. The knife overlap helps to provide you with a smoother surface and minimizes the size of chips. Thanks to increased hardness and the possibility of edge turning (HWM), the intervals between grinding are longer and also ensure a continuous planning readiness. When a knife is damaged or blunt, simply and quickly replace it or rotate for another sharp edge.
What were the evaluated parameters?
When evaluating, we focused on the quality of surface finish in problematic spots, the noise of the machine, how both blocks hold an edge and the associated resistance when feeding the workpiece into the cut. To test these out, we used new combined JET Machines JPT-310 a JPT-410 on the factory set-up. We only cleaned up the grease. As for the wood, we used 200 mm wide pine boards.
Quality of worked surface
Surface planed with HSS knives
Distinct traces of planing knives are visible along the entire width of the planed material. Opposite fibres around knags and in problematic spots are plucked out, somewhere the cut is even 0,8 mm deep. Otherwise, the surface is standardly planed.
In this case, the board is unusable and has to be ground to size or stuffed and ground (if the boards won’t be painted).
Both ways only prolong your work.
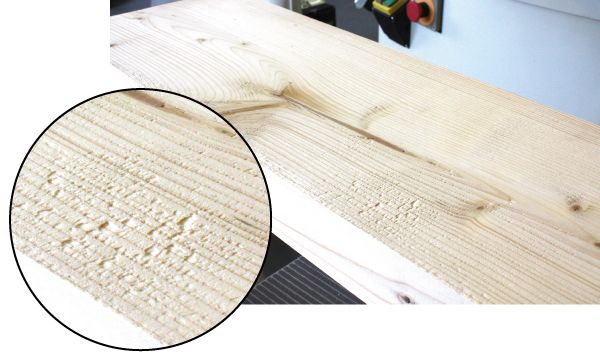
Surface planed with HW knives
The difference is visible at the first sight. The planed surface is beautifully smooth even in problematic places without any broken off chips or dents. There is no sign of planing along the entire width of the workpiece.
The only thing left to do is to grind the board with a 120G abrasive and start surfacing.
The surface is free of any visible knife strokes, which is common with spiral knife cutter heads. This is achieved by the radial edge of the knives, which the JET cutter block is fitted with.
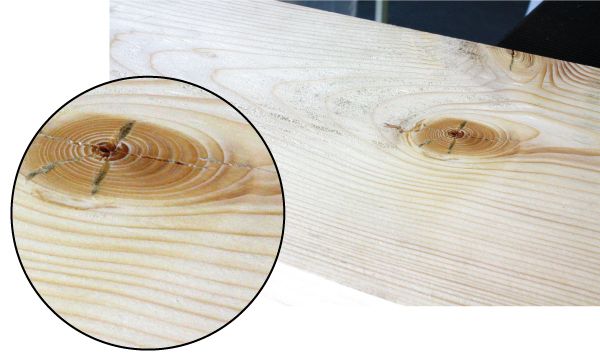
Noise
The noise of the machine may be best judged by the values listed in the manual and by your personal experience.
The noise level listed in the manual may differ according to the type of operation (planing or thicknessing) in idling or processing (idling or material removal). In general, however, it can be determined from the values in the manual and through feelings that a machine with a spiral set knives has half the noise level against planing cutter head with three HSS knives at idle speed and during removing material.
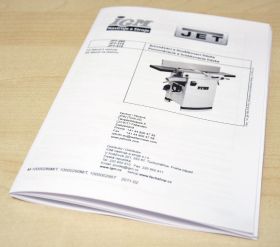
Example of noise levels
(According to EN3746):
Machine with HSS knives
Freewheel run LwA 89.8 db(A)
Operating speed LwA 101.8 db(A)
Machine with HW knives)
Freewheel run LwA 80.7 db(A)
Operating speed LwA 87.8 db(A)
If we compare these values on paper, we can find out the difference is especially significant when removing wood. Will it be so in reality? At first, we tested a machine fitted with the HW knife cutter block 410 mm wide, which is the largest version of a combined planer thicknesser from JET and we were very surprised, how silently can a 350 kg machine run. Against this, we tested the HSS knife fitted cutter block in the width of 310 mm and we couldn’t believe our ears. A larger and 100 mm wider machine is the silent one. The same happened when planing. The HW fitted cutter block is significantly quieter, which makes working with it far more comfortable.
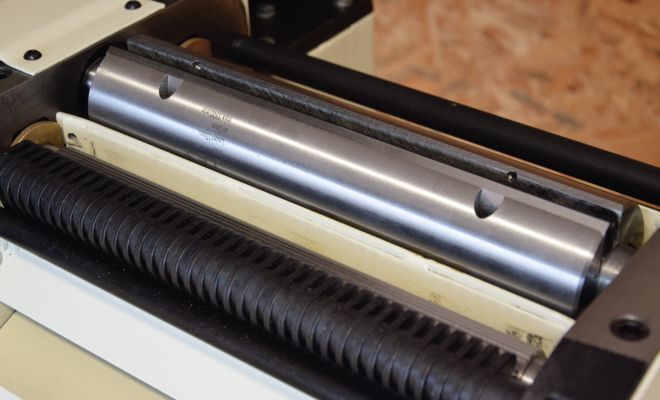
Edge life and overall impression
Unfortunately, for time reasons we weren’t able to fully test out how both knives hold their edge, that is why we will draw on the experience of the material used to manufacture these knives. At the moment the battle holds between the HSS knives made of so-called high-speed steel and HW knives made of hard wolframite.
The HSS knives are available in two versions: Wood and Wood PLUS, which is harder and lasts longer, despite this the HW knives last 4 times longer than the regular knives. The knives fitted in the JET machine used for today’s tests are supplied in a single hardness – 1650 HV10.
When using HSS knives, you usually don’t wear out the entire edge of the knife uniformly or the knife gets chipped, which is a disadvantage since you use the entire edge length and set of knives to plane to prevent uneven surfacing. The HW fitted cutter block is different though if a knife gets dulled or chipped you simply rotate it to form a new edge. When an HSS knife gets chipped or is dull, you have to replace it, sometimes along with the whole set. So you must always have spare knives. When using the HW knives, however, you simply rotate the knife and continue on with your work.
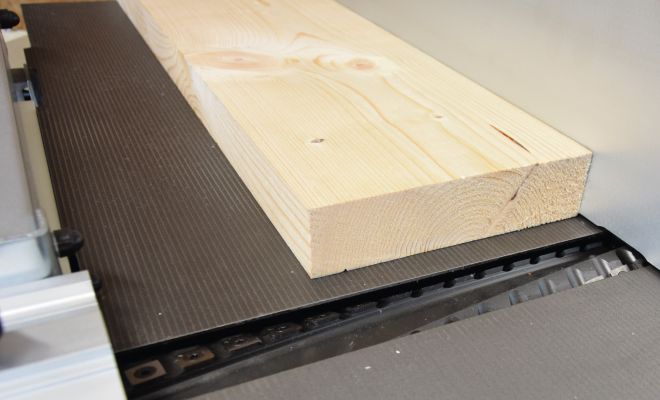
When assessing the difference between the mentioned knives, the divide becomes especially noticeable when working with different widths. The HW knives remove material with indescribable ease. The material is fed into the cut very easily and the overall impression definitely leans towards the cutter block fitted with spiral set HW knives.
HW and HSS knives in numbers
Sooner or later you will have to replace knives on both types of cutter heads. And as we have mentioned in the previous article, a complete comparison cannot be made. That is why we will try to calculate the operation cost of a 200 mm wide cutter block.
Overview of knives fitted on a regular combined machine:
400 mm long, 4 HSS knives. Even when using only 200 mm, in a case one of the knives gets damaged, you will have to replace all 4 knives.
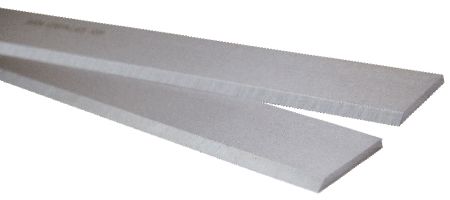
TheHW knives are 15x15 mm and there are 30 knives fitted for 200 mm. In a case on or more edges get damaged, you simply rotate the knives and continue on.
4x longer edge life and 4 edges on every knife provide a 16x better use than HSS knives.
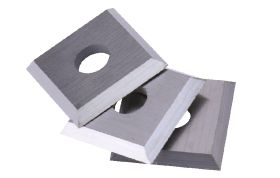
Example:
Price of 4 HSS knives: 1800 CZK without VAT
Price of knife sharpening: 374 CZK without VAT (all knives have to be sharpened along the entire edge)
Price for equipping a 200 mm cutter block with 30 knives: 4350 CZK without VAT
The theoretical life is set to 100m (only a theoretical number)!
HSS knives – average number of sharpening 20x
Theoretical life: 20x 100m = 2000 m
HW knives – 4x longer life and 4 edges on each knife
Theoretical life: 4 x 4 x 100m = 1600 m
Recount for 1m of planing:
Cutter block with HSS knives
Planed meters throughout the whole life: 2000m
Total costs: a set of knives 1800 CZK + price for sharpening 20 x 374 CZK = 7480 CZK
In total: (1800CZK + 7480CZK) / 2000m = 4,64 CZK/1m
Cutter block with HW knives
Planed meters throughout the whole life: 1600m
Total costs: 30 knives 4350 CZK
In total: 4350CZK / 1600m = 2,72 CZK/1m
There are various ways of fitting a cutter block with HSS knives, various prices of knives depending on the manufacturer etc. but even when considering these combinations, you are still able to save up to 40% by using the cutter block fitted with HW spiral set knives!
Conclusion
If we go back to the beginning of this article, we can understand the high number of professionals and craftsmen who use the HW fitted cutter block. Not only that the user experiences greater comfort and less noise when working, he even saves time by not having to continually replace knives with difficulty.
What is most surprising however is the 40% saving rate per meter in operating costs. That is an unbeatable argument.
All tests were performed using combined JET machines.
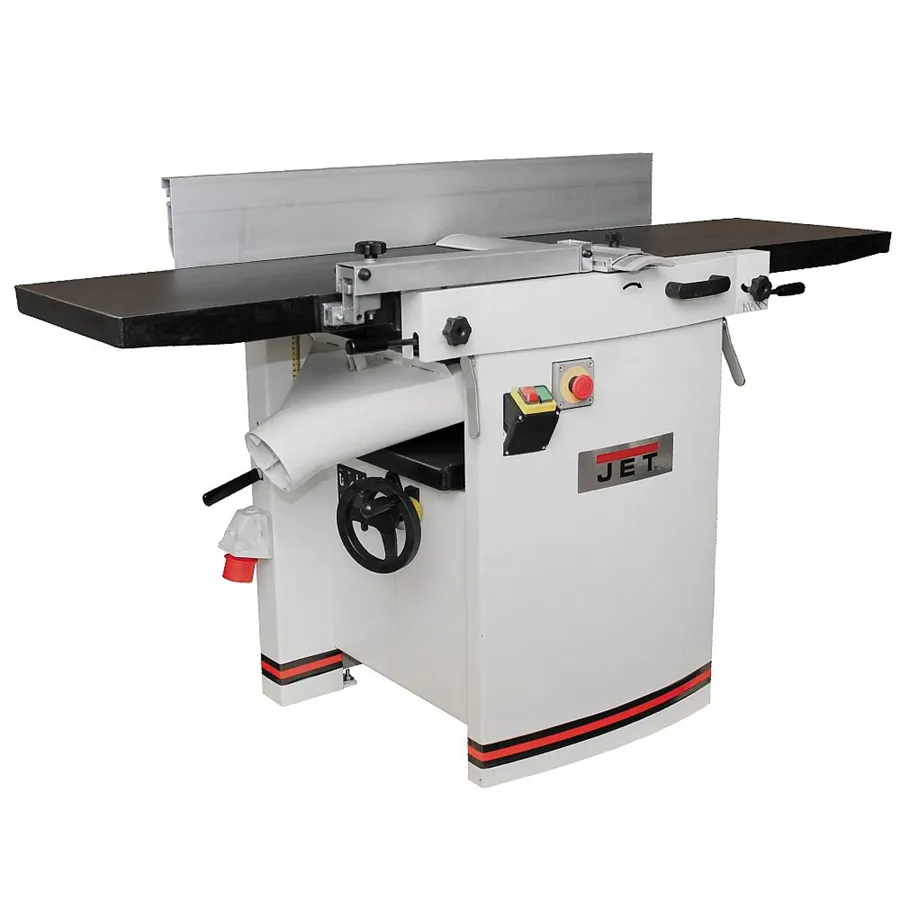
Visit our IGM store in Tucoměřice and check out the difference yourself.