CNC Spiral cutters with high feed rate
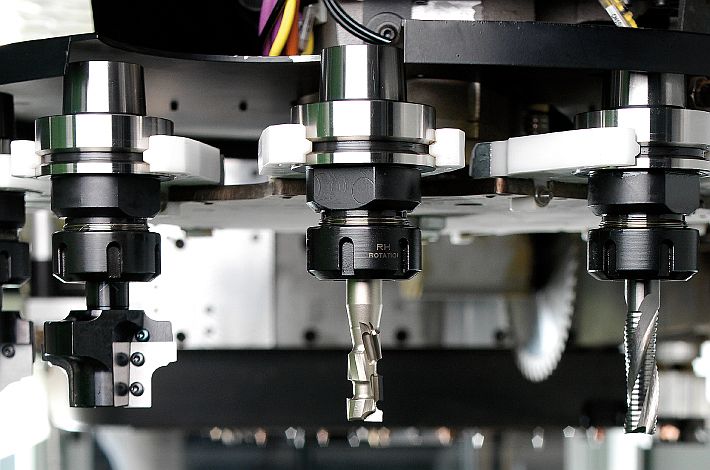
I often deal with customers who own a CNC router or a machining centre and they often ask me about the type of material and operation ideal for their spiral cutters. When should I use a cutter with chip breakers or a so-called smooth cutting edge? We will try to answer at least some inquiries about this issue and the use of individual spiral cutters.
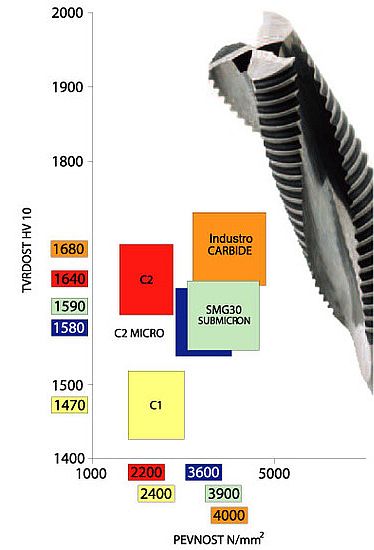
The body of the tool
It's important to mention what the spiral cutter is made of. All manufacturers claim their spiral cutters are made of HM material (carbide, tungsten carbide or simply HM) or HM integral (whole carbide, tool made of a single piece of material, made of bar material), but as we know, not all HM cutters are the same and it's therefore clever to make the right choice when selecting a manufacturer.
CMT uses carbide in bars (strength 1680 HV10 and hardness 4000 N/mm2.) for their spiral cutters. This means tools with long edge life and unique strength when compared to other manufacturers.
Tool construction
The body of the CMT spiral cutters is shaped on CNC grinders with emphasis on accuracy and tool functionality. The tool receives its efficiency from the precise grounding of the edge.
Grinding a radial edge with a deep recess for effective chip removal is essential. The radial front of the tooth helps the cutter to retain strength while achieving a rake angle up to 15%, which is important for routing along and through the grain (the rake angle depends on the diameter and number of edges on the tool).
Spiral grinding of the edge against the axis of the tool is an important part of the construction of the cutter. This shape helps to remove dust from the cut and provides a clean cut on the workpiece depending on the direction of the chip into or out of the cut.
What are chip breakers and what is their purpose?
Chipbreakers are often found on so-called roughing cutters and have an important function in improving the performance when routing. Chipbreakers are approximately 0,5 mm deep teeth shifted relative to each other.
These teeth will reduce chips resulting in less strain on the machine.
The whole aim is to increase the cutting power twofold. The performance will be altered by the firmness of worked material, depth of routing and the amount of material removed.
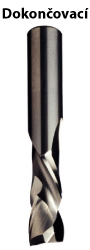
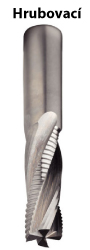
The difference between a spiral, roughing and finishing cutter (smooth tooth).
The main difference between a roughing and finishing cutter (smooth tooth) is on two levels.
• A roughing cutter will leave a roughed up surface with grooves app. 0,5 mm. Finishing cutter with a smooth tooth leaves a completely smooth surface.
• The roughing cutter achieves approximately 3x higher performance while saving time.
CMT spiral cutter - saves up to 30% of time
These individual properties of the roughing cutter and finishing cutter with smooth teeth make them ideal for combination work and routing of various cuts or formats.
First, a roughing cutter able to rout 3x faster and then a finishing cutter to clean up the surface and rout app. 1 mm to the exact size. You can also use the 3x faster feed to rout 1 mm to an exact size since the router removes only a small portion of material and accurately cleans up the surface. Thanks to the combination of these two operations, you can save up to 30% of time while securing unique results.
Worked materials
|
Tool - spiral cutters
|
Hardwood
|
IDEAL (construction and geometry is ideal for this material, minimum dull, clean cut)
|
Softwood
|
IDEAL (construction and geometry is ideal for this material, minimum dull, clean cut)
|
Plywood
|
IDEAL - SUITABLE (construction and geometry is ideal for this material, dulls more because of glue, clean cut)
|
DTD, LTD
|
IDEAL (construction and geometry is NOT ideal for this material, dulls quickly because of glues and laminates, clean cut)
|
Back to what's new