In this article, we will have a look at different types of
saw blades their characteristics, and differences in shape and number of teeth.
Classification of saw blades and their selection is widely discussed and understandably so, because saw blades are not always chosen for the right job. This article will help you choose a proper saw blade suited for your needs.
Basic classification of saw blades
Sheet metal saw blades
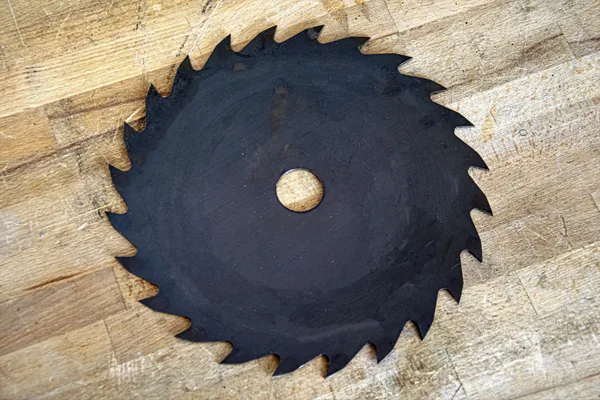
Saw blades with carbide teeth
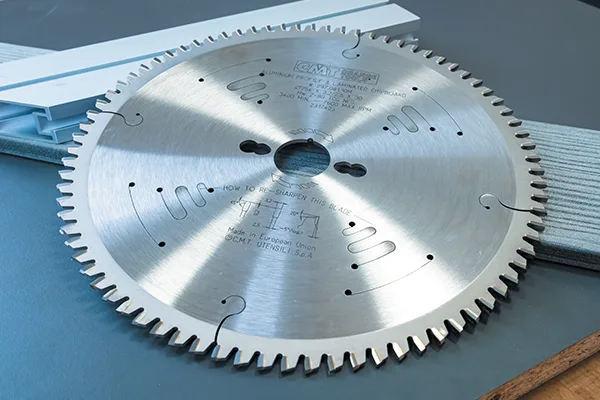
Because of their low cost, sheet metal saw blades are commonly used for cutting firewood or can be found on older saws. Their teeth are cut out of a steel plate, bent alternatively outward to the axis of the blade. Same teeth configuration is used on bandsaw blades, called staggered teeth. Tough steel makes teeth more resistant to breakage. Unfortunately, these teeth dull very quickly and make rough and imprecise cuts.
Saw blades with carbide teeth may also be called tungsten carbide or cemented carbide. However, they usually refer to the same material. Carbide is formed under high pressure and heat from a very fine mixture of metals, such as tungsten, cobalt, nickel, copper or iron. This alloy is several times harder than steel and is therefore used for manufacturing of woodworking tools.
If you want to achieve perfect results when cutting wood, you should always choose saw blades with carbide teeth.
However, carbide teeth do not necessarily guarantee a perfect cut and long life. You need to choose a proper saw blade for the job.
How to identify a proper saw blade?
Carbide tooth thickness
In hobby shops or non-specialized stores, you may come across cheaper carbide blades. At first glance you should already recognize major differences from professional blades. Carbide tooth thickness is essential, the thicker the tooth the better. Thicker teeth can be sharpened repeatedly allowing more sharpening cycles.
A professional blade has teeth 2,5-3 mm thick, a cheaper blade may have only 1-1,5 mm thick teeth. The thickness greatly influences blade durability. Cheaper blades usually have single-layer brazed teeth making them more prone to chip off from the blade. Additionally, such blades can be sharpened only a few times compared to professional blades. Professional blades allow up to 3x more sharpening cycles thanks to 3 mm thick teeth with three-layer brazing.
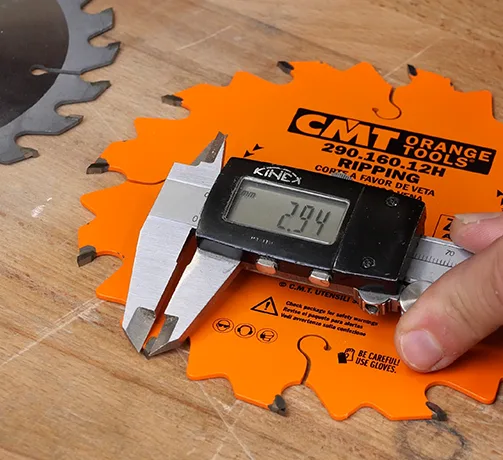
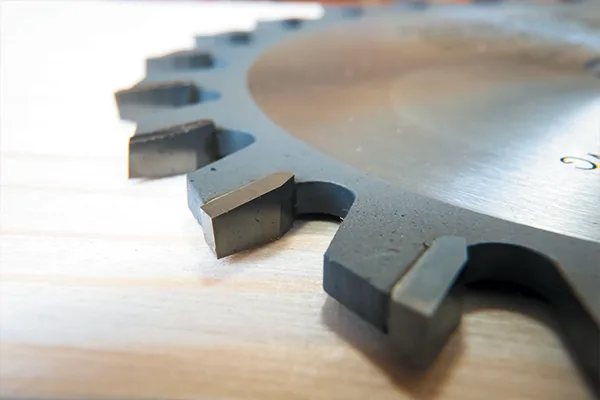
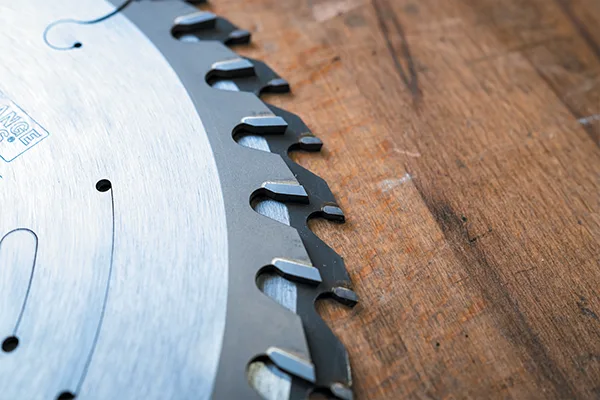
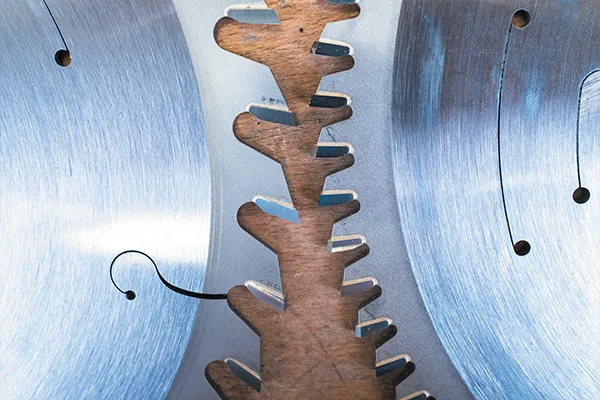
Saw blade surface
You should also keep an eye out for the blade body. If the surface is coarse to the touch, it generally means that sawdust, glue and resin residue can easily build up on the surface and the blade will rust quicker.
Surface of the blade should be smooth, ideally lacquered, coated with teflon or chrome.
Lacquered surface

Teflon surface

Chromed surface

Other important aspects
Other important aspects to look out for are sound-dampening and expansion slots on the blade body. The importance of slots is often overlooked. Slots are essential for better comfort and quality of the cut.
As the name implies, sound-dampening slots affect noise level, eliminating noise created by a rotating blade. You can simply test sound-dampening qualities of a blade by poking your finger through the middle and tapping it with a knuckle. If the blade resonates like a gong, it will make loud noise during work, such as whistling or humming. On the other hand, a blade with sound-dampening slots resonates very briefly when tapped.
Sound-dampening slots
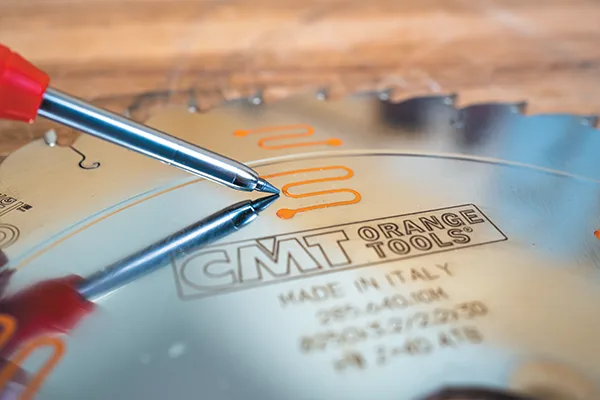
Expansion slots
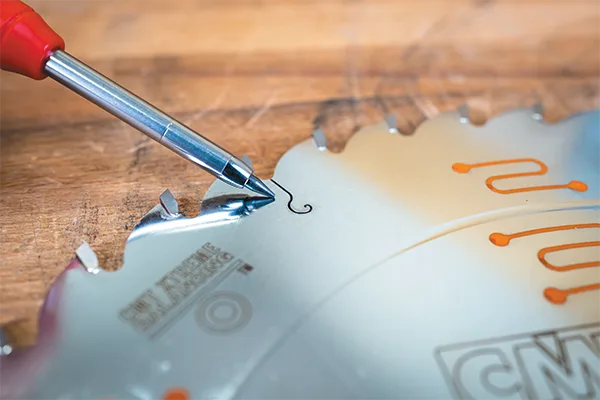
Expansion slots can be found around the edge of the blade between the teeth. These slots eliminate deformation of the blade that occurs due to heat. Simply put, a blade with expansion slots will not warp under heat opposed to a cheaper blade. Blades without expansions slots can produce a wavy cut and cause burn marks on wood.
Tensioning ring
A tensioning ring is applied on the blade by means of compressing between two tips. This ring ensures stability and perfect alignment during rotation. It also makes the blade stiffer preventing vibration.
With tensioning ring.
Without tensioning ring.
Basic classification of saw blades is also summarized in this video.
Classification of saw blades by tooth shape, number of teeth and rake angle
Tooth shapes, number of teeth and rake angle determine which material is the blade suited for.
When choosing a blade, you can come across different tooth configuration with different abbreviations, such as alternate top bevel, triple chip grind, flat, hollow, conical, or a combination of these. The most common shapes are alternate top bevel and triple chip grind.
Tooth shape
WZATB alternate top bevel
WZ N alternate top bevel, negative rake angle
LWZ alternate top bevel with chip limiter
SSWMATB alternate top bevel with chamfer grind
TFZTCGFFT triple chip grind alternating with flat top
TFZ N triple chip grind alternating with flat top, negative rake angle
FZFLAT flat top grind
FZ N flat top, negative rake angle
LFZ flat top with chip limiter
TZ triple chip grind
DHZHDF hollow face grind alternating with inverted V tooth
DHZ N hollow grind alternating with inverted V tooth, negative rake angle
HR hollow tooth
KONCO conical tooth
Alternate top bevel
The alternate top bevel is frequently used for cutting solid wood. As the name implies, this configuration has alternating bevels between each two teeth – to the right and left. The ATB is used for quick and aggressive cuts but is generally not suitable for slots. You can also find ATB blades for laminate or plywood, which have a very steep bevel. They are called high alternate top bevel (Hi-ATB). This shape results in a smoother cut on both sides of a material, such as laminate or veneered boards.
* K – tooth width / P – blade width / ß – bevel
Triple chip grind
The second most common configuration is the triple chip grind, forming a so-called trapezoidal shape. The tip of the tooth is flat with both edges bevelled. Blades with triple chip grind are combined with flat top grind, alternating between the two shapes. These blades are ideal for cutting large panels, such as laminate, MDF, compact boards, veneered boards, plywood or non-ferrous metals. Triple chip grind is not suitable for solid wood. It lacks the power of the alternate top bevel, causing tooth drag and burn marks when cutting solid wood.
* K – tooth width / P – blade width / ß – bevel / h – height difference of cutting edge between triple chip grind and flat top
Flat top grind
The third fairly commonly used shape is the flat top grind, typically found on dado & grooving saw blades and on scoring blades for panel saws. Although flat top has a relatively high tooth drag, it is made for cutting kerfs (slots cut in the material). The flat top is used for embedding hardboard, mouldings or glass in furniture and cutting tenon and butt joints.
* K – tooth width / P – blade width
Hollow grind
The hollow grind is barely used, mainly for cutting laminate with vertical saws without a scoring unit. You can find blades with hollow grind in custom cutting shops. The biggest disadvantage is a relatively high cost of sharpening.
* K – tooth width / P – blade width / R – radius
Conical tooth
The conical tooth can be found chiefly on scoring blades for panel saws. This shape is expanding top to bottom. You can extend the blade according to your needs, so you can cut narrow or wider slots.
* K min – min tooth width, K max – max tooth width
P – blade width / ß – bevel
Number of teeth
Another parameter you need to take into account is the number of teeth on the blade, usually labelled by the letter Z or T from English. The number of teeth is especially important when cutting solid wood. This number varies depending on the direction of the cut (rip cuts or cross cuts).
Follow this rule in general
Rip cuts are made by blades with less teeth, having a larger gap between them. This gap is called gullet. Less teeth and large gullets provide a quick cut and better chip flow.
For 160 mm diameter use saw blade with 12-18 teeth.
For 250 mm diameter use saw blade with up to 30 teeth.
S – material thickness, H – tooth height above the workpiece, P – teeth pitch
Cross cuts are made by blades with more teeth, having a smaller gullet between. Small gullets eliminate splintering and burrs while more teeth ensure a smooth cut.
For 160 mm diameter use a blade with 48-56 teeth.
For 250 mm diameter use a blade with 60-80 teeth.
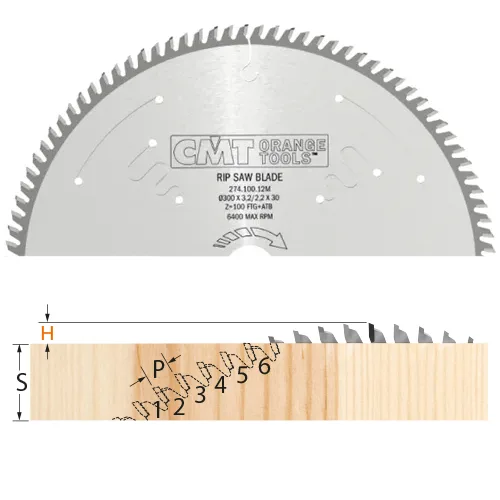
Universal saw blade for rip and cross cuts
Saw blades with tradeoffs that provide a perfect middle ground.
DIY woodworkers most often look for one universal blade for every job. Such a blade is available but features many tradeoffs compared to solely cross cut or rip cut blades. Universal saw blade should not have too many teeth to perform rip cuts easily, but also cannot have too few teeth which cause splintering and burrs.
For 160 mm diameter use a blade with around 24 teeth.
For 250 mm diameter use a blade with 40-48 teeth.
Mentioned tradeoffs are: Slower rip cuts, slight splintering when cross cutting.
Rake angle (hook angle)
The rake angle can be positive, negative or zero. A positive rake angle means that the teeth lean in the direction of blade rotation, while a negative angle means that the teeth lean against the direction of blade rotation.
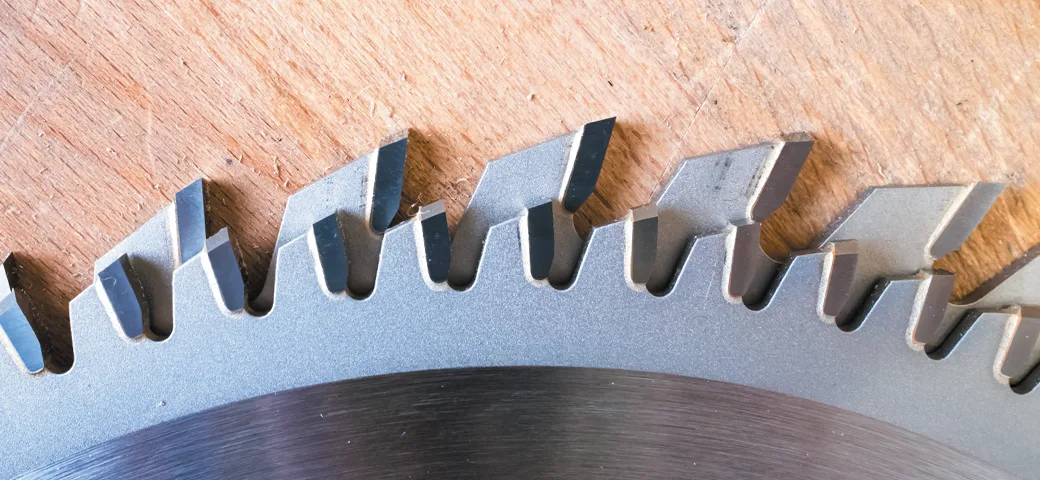
Positive rake angle speeds up the feed rate, delivering a quick and aggressive cut. It is ideal for cutting solid wood, plywood, laminate and MDF boards on panel saws with a scoring unit.
α = 10°~25° - Wood
α = 5°~15° - Chipboard, MDF, plywood, laminate, plastic
α = 0°~10° - Chipboard, MDF, non-ferrous metal, ferrous metal
Negative rake angle is used mainly when cutting non-ferrous metals, plastic, compact boards, floating floors and Plexiglas. A tooth with negative rake angle cuts gradually into the material, slowing down the feed rate but creating a precise and smooth cut. The negative rake angle can be found on mitre saw blades in combination with an alternate top bevel. That is because of requirements for maximum versatility for cuts in solid wood, laminate or even aluminum. It is also suitable for plunge saws when cutting laminated boards without a scoring unit.
α = -5° ~ -15° - Ferrous metals, non-ferrous metals, plastic, laminate.
Zero rake angle is commonly used for cutting Corian and thick plastic. α = 0°
Different types of saw blades are shown in this video.
Cut demonstration
You can verify everything you have learned in the following video, in which we demonstrate that cutting solid wood with a blade for laminated boards is not a good idea. You can also see how the cut looks using a proper saw blade or how some blades are not really made for certain materials.
Perfect cut, smooth and straight without burrs.
Wrong saw blade for laminates. Splintered laminated board.
This is how the cut is supposed to look. Minimal burrs, smooth and precise cut.
Triple chip grind teeth should not be used on solid wood. Burn marks.
Demonstration of different saw blades affecting some materials is summarized in this video.
Category Saw Blades